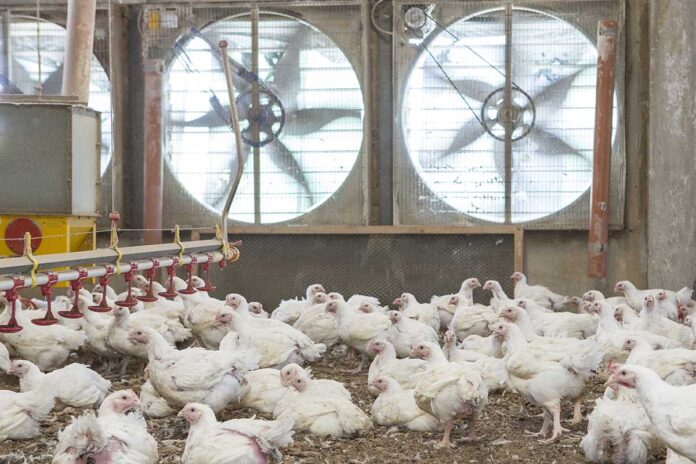
Gli articoli tratti dalla serie di webinar che su questo tema ha organizzato il Department of Poultry Science della University of Georgia si concludono con un’analisi dei problemi legati alla ventilazione forzata.
Nei moderni capannoni avicoli si utilizza spesso una ventilazione forzata: in questo sistema il nodo essenziale non è quello di fornire una ventilazione massima, ma piuttosto quello di stabilire quella minima, al fine di evitare sprechi di energia per il riscaldamento, correnti fredde sugli animali nonché bruschi e pericolosi cali di temperatura ambientale.
Esistono varie tipologie di ventilazione: quella naturale, o con finestre, può essere efficace in climi moderati, in presenza di soggetti adulti e con differenze termiche minime tra interno ed esterno.
In presenza di climi freddi, invece, diventa difficile regolare una costante immissione di aria fresca. Con le finestre aperte, infatti, non si riesce a controllare il ricambio di aria per varie cause (ad esempio per la presenza di polvere e ragnatele che coprono le reti antipassero, ostruendo di fatto le aperture). Inoltre la distribuzione dell’aria in entrata è poco uniforme e i soggetti più vicini alle finestre sono più esposti all’aria rispetto a quelli che si trovano al centro del capannone. Infine, l’aria esterna fredda, essendo più pesante di quella calda nel capannone, appena entrata si dirige direttamente verso terra, raffreddando i polli, senza miscelarsi correttamente a quella calda che si trova naturalmente nelle zone alte del capannone. In tal modo i polli non solo si raffreddano, ma l’aria che scende sulla lettiera, ancora fredda, ha una limitata capacità di assorbire umidità, e quindi non riesce ad asciugarla correttamente.
Stabilire una corretta pressione negativa
Se vogliamo controllare meglio lo scambio e la distribuzione dell’aria, dobbiamo quindi impostare una ventilazione forzata, meglio se basata su una pressione negativa, nella quale i ventilatori regolano la quantità del ricambio di aria in uscita, mentre gli ingressi dell’aria controllano al meglio la sua distribuzione e miscelazione. Avere a disposizione ventilatori e ingressi di aria regolabili non basta però a controllare correttamente il ricambio e la distribuzione di aria.
Infatti, se non si stabilisce una pressione negativa corretta nel capannone, si rischia di immettere troppo velocemente aria fredda che, senza distribuirsi bene all’interno, esce riscaldata, passando per il soffitto, e lasciando così l’ambiente sottostante immodificato e statico.
Bisogna pertanto evitare correnti e distribuzione dell’aria a macchie nel capannone, sia come stratificazione che a livello di lettiera, con zone più fredde e altre più calde. Infatti in quest’ultimo caso i soggetti si posizionano nelle zone più confortevoli, bagnando maggiormente la lettiera, mentre altre aree restano completamente libere: di fatto la densità per metro quadrato aumenta nelle zone più affollate e diminuisce in quelle vuote.
Se invece si ottiene una corretta pressione negativa, attraverso la gestione degli ingressi dell’aria insieme ai ventilatori, questa resterà la stessa in tutto il capannone, indipendentemente dalle sue dimensioni. Ciò significa che l’aria estratta dai ventilatori entra ugualmente da tutti gli ingressi di aria, senza creare delle differenze ambientali.
È possibile rilevare la presenza di pressione negativa con facilità: se le fenestrature sono realizzate in telo plastico, questo viene lievemente risucchiato verso l’interno e le porte sbattono quando le si chiude. Fare una prova pratica è piuttosto semplice: è sufficiente infilare in un ingresso di aria un tubino di plastica trasparente, immerso da un lato in un bicchiere di acqua. Se si nota un innalzamento del livello dopo l’inserimento, significa che internamente è presente una pressione negativa, che risucchia l’acqua di alcuni millimetri: questo livello aumenterà con una pressione negativa crescente. Se invece si desidera ottenere una valutazione più tecnica, si può usare un misuratore di pressione.
Il livello di pressione negativa deriva sia dal numero e dalla velocità dei ventilatori in estrazione (se sono molti aumenta la pressione negativa e viceversa), che dall’apertura delle finestre. Per misurare la velocità dell’aria in ingresso, si usa un anemometro posto vicino agli ingressi di aria: maggiore sarà la quota di aria estratta, maggiore la pressione negativa che si crea, e quindi maggiore sarà la velocità di aria in ingresso.
Il crearsi di una pressione negativa nel capannone garantisce che da ciascun ingresso di aria la quantità e velocità siano le stesse, creando di conseguenza un ambiente uniforme. L’aumento o la diminuzione del volume di aria estratta avrà i medesimi parametri dappertutto, indipendentemente dalla distanza delle finestre dai ventilatori. Ciò è importante, perché altrimenti, senza pressione negativa, l’aria entra naturalmente con maggiore volume e velocità dagli ingressi più vicini ai ventilatori, creando un ambiente disomogeneo, con aree calde o fredde, e relative correnti sugli animali.
Controllare la velocità di ingresso dell’aria consente di farla entrare con forza, tramite apposite aperture, convogliandola verso il soffitto dove si trova quella calda, permettendo di miscelarsi ad essa riscaldandosi, e di scendere infine sui polli, portando ossigeno e rimuovendo, al contempo, umidità e gas nocivi.
Le aperture
Una pressione negativa da sola non è sufficiente: occorre anche disporre di ingressi di aria corretti, in grado di aumentare e diminuire l’apertura a seconda delle richieste ambientali e dell’attivazione dei ventilatori, e di direzionare l’aria dove si vuole, quindi verso l’alto. Una volta si usavano piccole aperture, realizzate abbassando di poco la fenestratura laterale, che però creavano un ambiente poco uniforme: l’aria sul soffitto rimaneva calda, mentre erano evidenti gli sbalzi termici a livello degli animali. In seguito si sono adottate diverse tipologie di finestrelle ad apertura variabile, in grado di dosare sempre correttamente il flusso, la velocità e la direzione dell’aria in ingresso. Semplici strumentazioni, come l’uso di fumiganti o di fotografie a ultrarossi, oggi consentono di vedere dove si distribuiscono aria e calore, verificando la correttezza della ventilazione.
Il numero di ingressi di aria di un capannone dipende ovviamente sia dalla quantità e dalla capacità dei ventilatori che dal ricambio che si desidera ottenere, in termini di metri cubi/ora. Di solito l’obiettivo è ottenere una pressione negativa di 0,10 pollici, misurata tramite un apposito lettore di pressione, riferendosi a un rapporto tra ricambio di aria, densità degli animali e superficie del capannone.
Ovviamente le richieste di ricambio di aria e quindi di ventilazione minima sono diverse in base alle diverse età e al diverso peso dei polli: in pulcinaia occorrerà calcolare il calore e il gas prodotti dalle cappe; poi, a seconda del peso e della densità, aumenterà il metabolismo dei pulcini e di conseguenza il volume dei ricambi di aria. Parimenti ciò avviene se le temperature esterne crescono.
Pertanto, conoscendo peso e densità di accasamento dei polli, si può valutare il calore da essi prodotto, da disperdere con la ventilazione, regolandola di conseguenza: su polli adulti si calcola all’incirca, per ogni metro quadrato di superficie, una ventilazione di 5 metri cubi di ricambio.
Conclusioni
Riassumendo, la pressione negativa, una volta instaurata, è la medesima in tutto il capannone: essa dipende dalla velocità di ingresso dell’aria nel capannone, secondo un rapporto non lineare. Possiamo valutare che in un metro quadrato di apertura entreranno 750 metri cubi di aria, mantenendo una pressione negativa di 0,10 pollici. Il minimo cui riferirsi è in genere di 5 metri cubi di ricambio per metro quadrato di spazio interno del capannone. Ricordiamo infine che polli e pollastre hanno peso e metabolismo assai diverso: queste ultime necessitano di circa il 40% di ventilazione in meno, mentre i tacchini, con metabolismo più accelerato, abbisognano al contrario del 35% in più di ricambio di aria.
Tratto da “2021 UGA Cold Weather Poultry House Ventilation System Principles, Design, and Operation Seminar”, University of Georgia, College of Agricultural & Environmental Sciences, Department of Poultry Science.