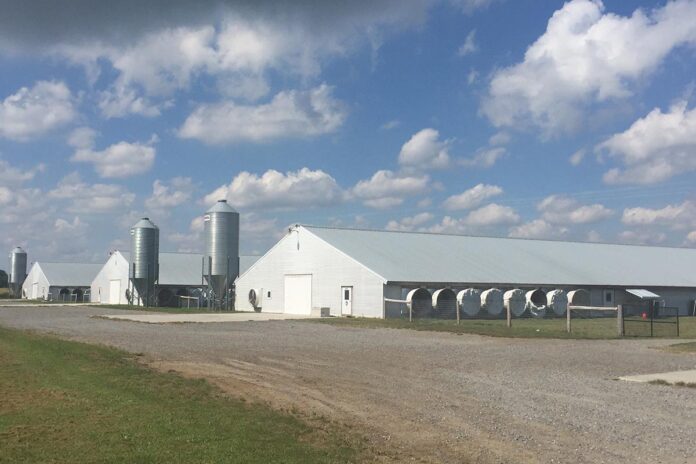
Prosegue il ciclo di report dedicati alla ventilazione tratti dai seminari del Department of Poultry Science della University of Georgia. In questo articolo viene affrontato il tema del controllo di alcuni gas all’interno dei capannoni avicoli.
Nei capannoni avicoli esistono diversi tipi di ventilazione; una delle più frequenti è quella a tunnel. Spesso si crede che la ventilazione dei capannoni serva per fornire ai polli l’ossigeno (O2) necessario, ma ciò non è del tutto vero: teoricamente, infatti, basterebbero pochi ventilatori per supplire a questa necessità, mentre di fatto ne usiamo molti di più. A titolo di esempio, per fornire l’ossigeno necessario a un capannone da 25.000 polli a fine carriera sarebbe sufficiente un ricambio di aria pari a quello della cappa ventilante di una normale cucina. Alcuni obiettano che con questa ventilazione non si raggiungono i livelli ematici di ossigeno necessari agli animali, ma bisogna ricordare che questo parametro non è legato all’ossigeno ambientale, bensì alla elevata presenza di monossido di carbonio (CO).
Presenza di monossido di carbonio (CO)
L’emoglobina, infatti, ha un’affinità 200 volte maggiore per il monossido di carbonio che per l’ossigeno. Quindi se i livelli di CO sono elevati, il sangue si lega ad esso e non all’O2, creando così una carenza di ossigeno. Un’esposizione alla CO di 600 ppm per 30 minuti causa stress, mentre a 3.000 ppm è letale. Una presenza costante di 70 ppm CO sembra inoltre che sia causa di ascite; andrebbe dunque mantenuta a livelli inferiori alle 50 ppm.
Ma come si forma la CO? Spesso troviamo livelli elevati di monossido di carbonio in zone con clima freddo, con il capannone chiuso e alti costi di riscaldamento, dove l’allevatore ventila poco cercando di risparmiare. Ma il monossido di carbonio cresce soprattutto in presenza di cappe mal gestite: la fiamma dovrebbe essere di colore rosso o blu, quando si nota una fiamma gialla verosimilmente il suo funzionamento è scorretto e pertanto genera CO. Un segnale di allarme potrebbe essere anche il colore del soffitto del capannone: se i fumi generati lo colorano di nero significa che la cappa non funziona bene. Per questo è importante, prima di far entrare i pulcini nel capannone, controllare ciascuna cappa, usando un apposito rilevatore di CO. Bisogna anche considerare il fatto che un tasso elevato di CO, oltre a essere nocivo per gli animali, è pericoloso anche per tecnici e allevatori che talvolta, se restano a lungo nel capannone, hanno mal di testa, proprio a causa della CO elevata.
Anidride carbonica (CO2) meno pericolosa del CO
L’anidride carbonica (CO2), che spesso viene indicata da linee giuda e normative come un dato importante di cui tenere conto – tanto che se ne definiscono i limiti massimi a 3.000 ppm – di fatto causa assai meno problemi di benessere e rese al pollo rispetto alla CO.
Secondo alcuni recenti studi, livelli di CO2 di 3.000, 6.000, 9.000 ppm non hanno evidenziato modifiche significative dei livelli ematici e neppure di crescita e conversione: le performance sono risultate immutate. Si è notato però un aumento di mortalità (ma solo a un livello di 9.000 ppm), legata a ipertensione polmonare. Si consiglia quindi di non superare livelli di 5.000 ppm.
La ventilazione necessaria a mantenere i livelli di CO2 inferiori a 5.000 ppm in un capannone di polli non richiede ricambi così elevati ed è facile da raggiungere. Diventa però più complesso se si vogliono raggiungere livelli inferiori: per arrivare a 4.000 ppm va aumentata del 29%, per 3.000 ppm dell’83%, mentre se si vuole restare sotto ai 2.000 ppm va aumentata del 214% e sotto ai 1.000 ppm addirittura del 1000%!
Considerato che l’80% dei costi del riscaldamento dipende dalla ventilazione minima impostata, se si vogliono mantenere livelli di 1.000 ppm occorrerà ventilare moltissimo, con una spesa altrettanto elevata. Pertanto i livelli consigliabili sono di 5.000 ppm (livello massimo) e di 3.000 ppm (livello normale).
Ammoniaca (NH3) e controllo dell’umidità
L’altro parametro, forse più importante di tutti, da tenere sotto controllo in un capannone avicolo è l’ammoniaca, per rimuovere la quale bisogna settare una ventilazione corretta. Infatti, già a 25 ppm l’NH3 causa una diminuzione delle performance (minore crescita, resa in fesa e peggiore conversione); se aumenta fino a 50-75 ppm i danni crescono proporzionalmente.
Ventilare per rimuovere l’ammoniaca, però, come abbiamo visto nello scorso numero di Zootecnica International (12/2021), non è conveniente: è molto meglio tenere asciutta la lettiera, in modo da evitarne la formazione. La ventilazione serve anche a ridurre l’umidità relativa del capannone (RH): se la si tiene sotto controllo, infatti, diminuisce il tasso di ammoniaca e migliora il benessere del pollo. L’eccesso di umidità non solo aumenta l’ammoniaca, ma anche i coccidi e peggiora la qualità del plantare, aumenta i problemi di gambe e respiratori, ecc.
Conclusioni
Riassumendo, fornire l’ossigeno necessario in un capannone avicolo non costituisce un problema, mentre è molto più importante l’efficace rimozione dell’umidità. CO2 e CO, infine, vanno monitorati costantemente, per mantenerli entro i limiti indicati.
Tratto da “2021 UGA Cold Weather Poultry House Ventilation System Principles, Design, and Operation Seminar”, University of Georgia, College of Agricultural & Environmental Sciences, Department of Poultry Science.